Step 1 of 7: Guide to Creating the Best Maintenance Work Order Planning Process and Procedure
The Maintenance Planner's job is to follow the Maintenance Work Order Planning Process and ensure there's a complete Work Pack for every Maintenance Work Order
A Maintenance Planner needs a Maintenance Work Order Planning Process to use that they know effectively and efficiently ensures every work order they plan gets a fully comprehensive Work Pack. The Work Pack explains how the maintainers will safely, correctly, and quickly complete the job and guarantee the equipment is highly reliable.
This post is the first of several posts to come about using the PWWEAM methodology to create a highly successful and productive maintenance work order planning process and procedure for Maintenance Planners.
Start with what people knowledgeable in planning successful maintenance jobs know
All PWWEAM process and procedure creation start the same way: with a blank sheet of A4 paper in front of a subject matter expert (SME) on which they describe the process design requirements.
A suitable subject matter expert for designing a maintenance job planning process is a person with at least 5-years recent experience in the maintenance planning role within the industry. Other suitable SME’s are a maintenance team supervisor with at least 5-years recent experience in the maintenance team supervision role within the industry; a maintenance manager with at least 5-years recent experience in the maintenance management role within the industry; a maintenance engineer with at least 5-years recent experience in the maintenance engineering role within the industry; a maintenance management consultant with at least 5-years recent maintenance processes experience relevant to the industry.
On the blank sheet of paper, list each key step a Maintenance Planner needs to consider and action, if required, in planning how to complete a maintenance work order for a challenging job. A hand-written example of a key-steps maintenance job planning requirements list is shown below. Don’t worry if a key step is left off the list. What is missed will be identified and included into the process during the detailed procedure writing stage.
Flowchart the Maintenance Job Planning Process steps
The key-steps list is then turned into a flowchart in a spreadsheet. This spreadsheet will be expanded and enhanced as you work your way through designing and building the Maintenance Work Order Planning Process and its procedure.

If you already have a maintenance job planning process and/or maintenance job planning procedure, convert their key-steps into a flowchart.
Describe the core Maintenance Work Order Planning Procedure tasks for each step
Under each step, include the key procedural tasks and outputs needed to complete that step. The full details of all tasks and activities done in each step will be explained in the yet to be written maintenance work order planning procedure. At this point, it is sufficient to note in the spreadsheet each step’s vital tasks and outcomes.
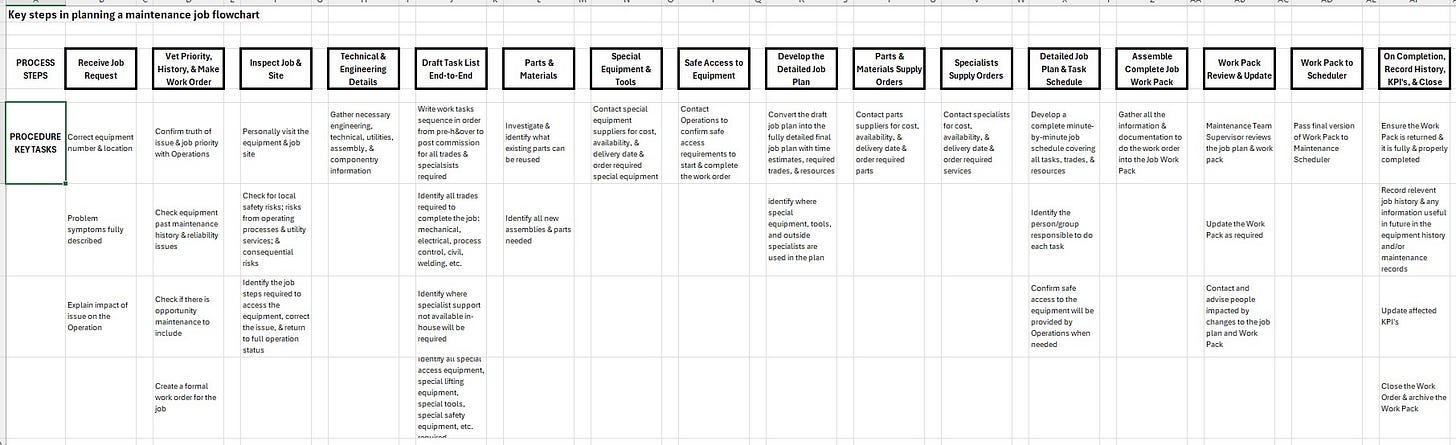
If you already have a maintenance job planning process and/or maintenance job planning procedure, include the key tasks done at each step into the flowchart.
In the expanded spreadsheet, you now have the core steps of a Maintenance Work Order Planning Process along with the fundamental procedure to be followed by the Maintenance Planner. The core procedure will be expanded into a documented maintenance work order planning procedure with all details the Maintenance Planner needs to know and do to build greatly useful Work Packs. You can download the above example process flowchart with key procedural tasks for your reference using the button below.
The process and its procedure are followed because they are the best way known to do maintenance work order planning
The Maintenance Work Order Planning Process is a live document, meaning it is updated in real time as new information becomes available and experience from its use leads to better or faster ways of doing maintenance planning tasks. The Maintenance Work Order Planning Process and its procedure are always kept current and accurate. They are the best way known in your organization to plan and resource maintenance jobs.
In the next post, we will cover writing the fully detailed maintenance job planning procedure. You’ll see how to make sure that each process step’s tasks are defined and clarified into the individual activities needed to compile a top-class maintenance work pack for a job.
If you want to jump ahead to learn more about building highly successful maintenance processes and procedures, you can get the Industrial and Manufacturing Wellness book, from the publisher, Industrial Press. It explains the PWWEAM methodology. Otherwise, keep getting this series of newsletters in which each one details a key aspect of creating a maintenance job planning process and procedure. When all are published, they will combine to fully cover the PWWEAM methodology for creating outstandingly successful maintenance processes and procedures.
Let me know if you have any questions on the above.