Step 3 of 7: Guide to Creating the Best Maintenance Work Order Planning Process and Procedure
Flowchart the Maintenance Work Order Planning and Resourcing Procedure to Turn Its Written Descriptions and Explanations into an Easy to Follow Step-by-Step Map
This week’s PWWEAM Substack newsletter and installment covers Step 3 of the Guide to Creating the Best Maintenance Work Order Planning Process and Procedure.
The purpose of the Maintenance Work Order Planning and Resourcing Procedure is to fully describe how to create and build the best Work Pack to do a maintenance job right first time. The procedure document is long and wordy because its function is to explain every activity that a Maintenance Planner might possibly need to do to assemble the best Work Pack.
Turn the maintenance work order planning procedure into a map people follow
It’s vital for Planners to understand and use the procedure, since it is the current best way known to build the best Work Packs. But the large amount of text and the complexity of the procedure’s workflow interactions turns people off of reading it and following it. To help Planners understand and do the procedure, its words are made into a map the Planner follows, activity by activity, to assemble a great maintenance job work pack.
Mapping the procedure and the workflow interactions is done in a flowchart showing the tasks and their activities in the order to be performed by the Planner. Two types of diagrams are used: a workflow diagram, and a deployment diagram. Examples of each are shown in the photographs below.
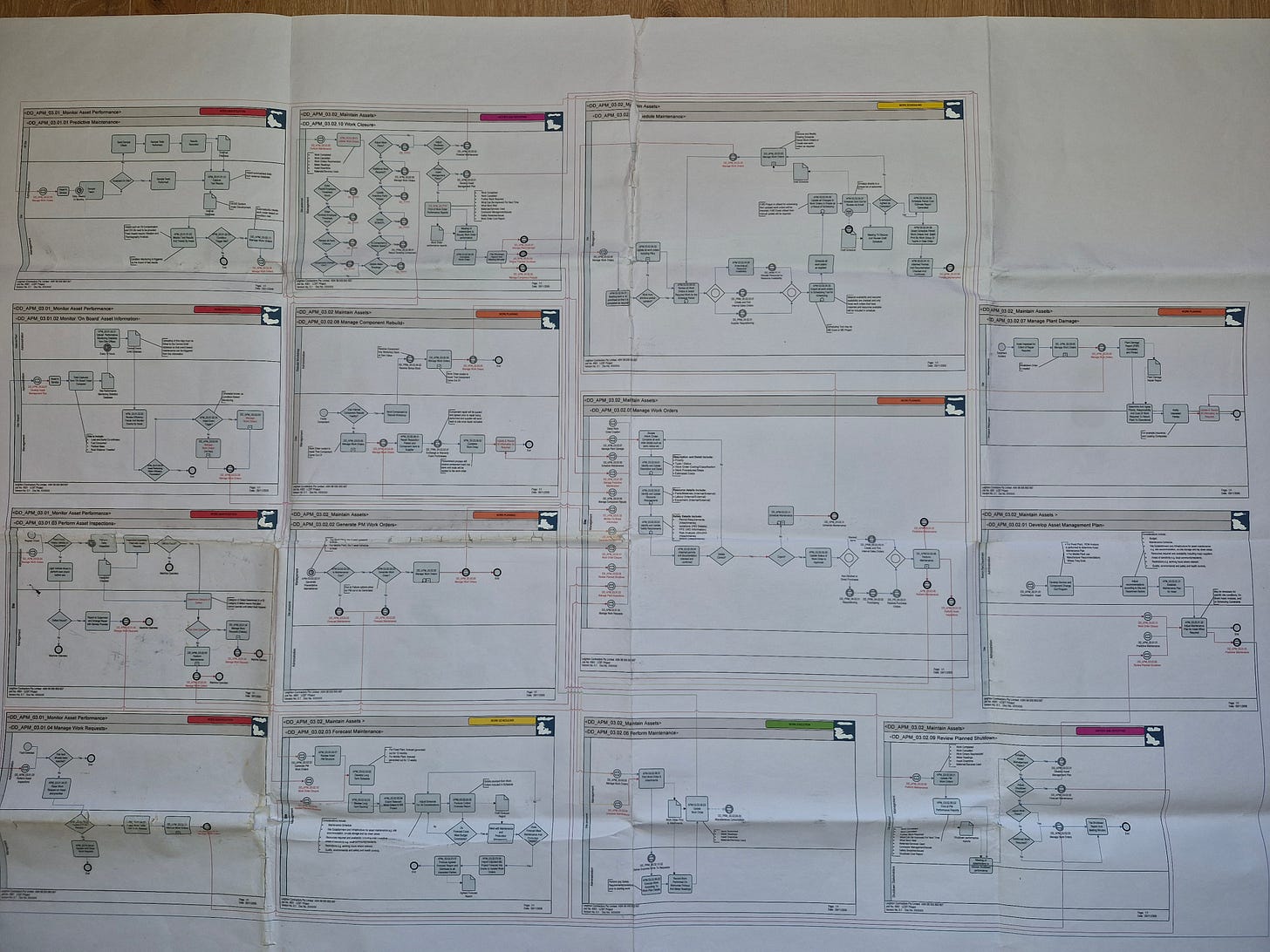
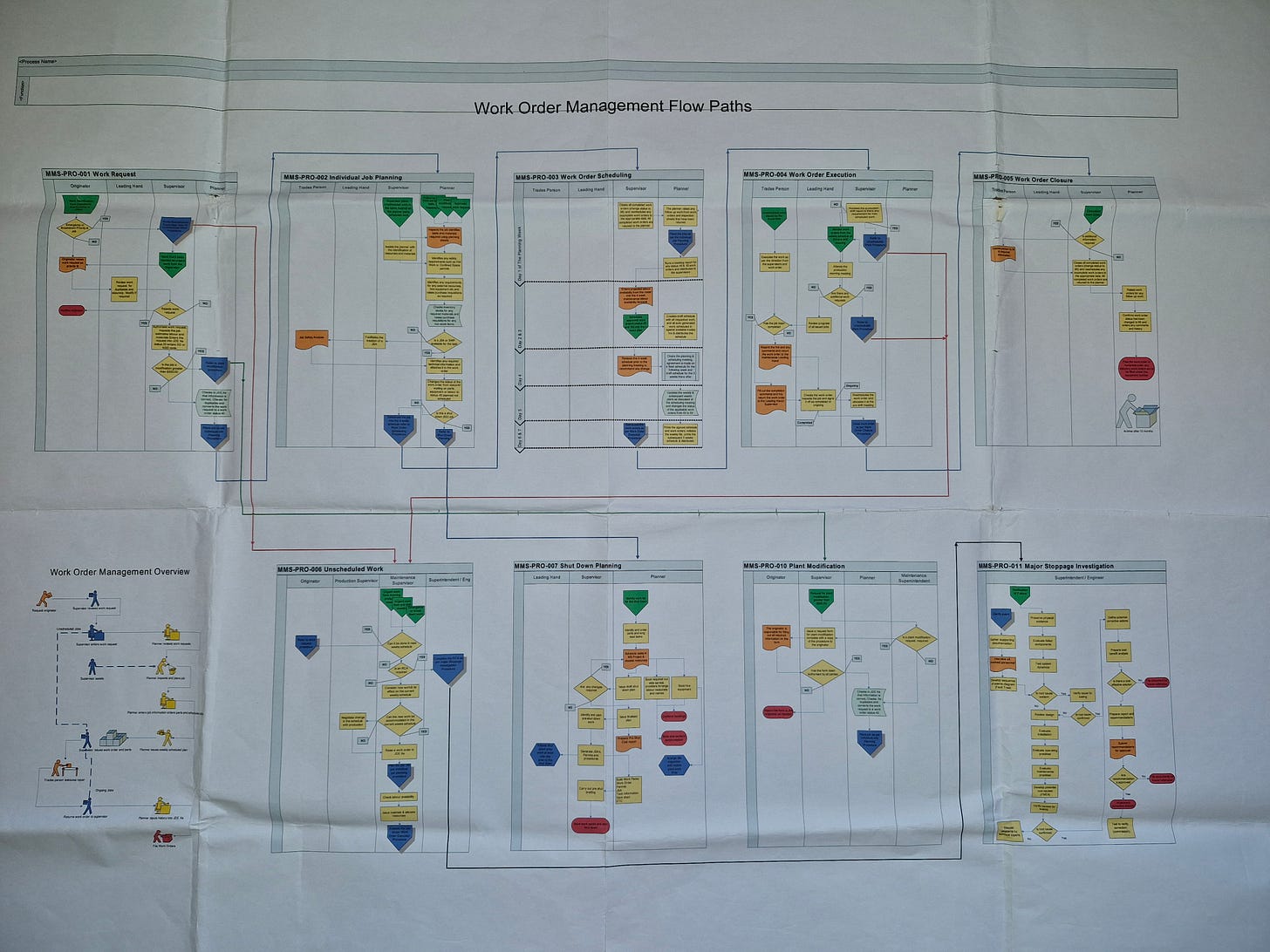
These diagrams are developed from the procedure by reading through its content and mapping all actions required to be done onto a workflow diagram. All personnel with responsibilities for doing them are shown on a deployment diagram.
Mapping helps identify if an action or a requirement is missing, or if the workflow is unclear, or if the procedure is wrong, or a step contains high risks to its successful accomplishment. In such cases, the procedure and process are revised and updated to address the matter, then approved and reissued to the Planners.
Next Week: Gauging the Chance Your Maintenance Planning Procedure Will NOT Be Done Successfully
Next week, Step 4 of the Guide will explain the unique approached used in PWWEAM methodology to measure the chance your maintenance job planning and resourcing procedure will be, and will not be, successfully done. Measuring the chance of successfully doing processes is one of the greatest innovations that the PWWEAM methodology brings to organizations.
If you want more information about building highly successful maintenance processes and procedures with the PWWEAM methodology, get the Industrial and Manufacturing Wellness book, from the publisher, Industrial Press. Otherwise, subscribe to this series of weekly guidance newsletters on creating a top class maintenance job planning process and resourcing procedure. When all are published, they’ll combine to help you master how to develop and write success-bringing maintenance processes and procedures with PWWEAM methodology.
Let me know if you have any questions.